A szilícium-karbid tűzálló téglák bemutatása
Silicon carbide refractory bricks are made of silicon carbide as the main raw material. SiC is covalently bonded and does not have the so-called sinterability. Instead, it relies on chemical reactions to generate new phases to achieve sintering, vagyis, reakció szinterezés.
According to different bonding methods, silicon carbide bricks are divided into clay-bonded silicon carbide bricks, bonded silicon carbide bricks, silicon oxynitride-bonded silicon carbide bricks, silicon nitride-bonded silicon carbide bricks, Sialon-bonded silicon carbide bricks, and recrystallized silicon carbide bricks.
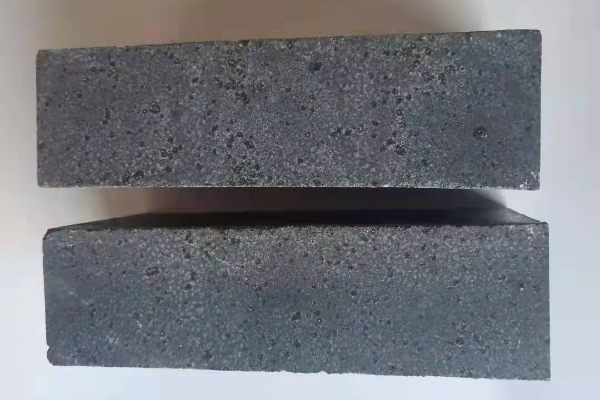
Different combination methods of silicon carbide refractory bricks
Clay-bonded silicon carbide fire bricks
Clay-bonded silicon carbide bricks are made of black silicon carbide as raw material, soft clay with good bonding properties, and pulp waste liquid as a bonding agent. Általában, it is combined with 10% to 15% of clay and 3% to 5% of pulp waste liquid. The maximum bulk density is used to calculate the composition of large, medium, and fine particles of silicon carbide.
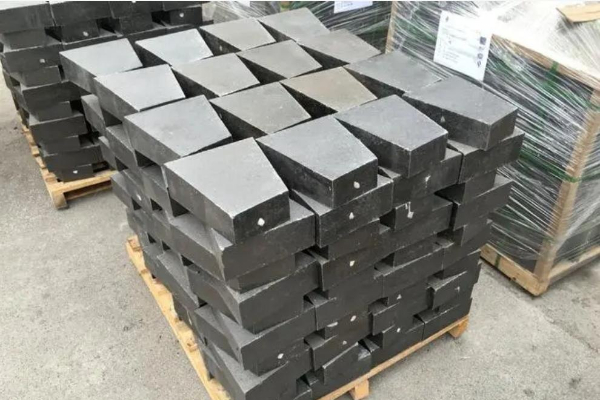
Silicon nitride-bonded silicon carbide bricks
Silicon nitride-bonded silicon carbide bricks are made of silicon carbide and silicon powder as raw materials and are nitrided and fired products.
The silicon carbide raw material contains more than 97% Sic, and the silicon carbide particle ratio of the mud material is: coarse: medium: fine = 5:1:4. Silica powder contains more than 98%, more than 80% is less than 10 μm, and the largest particle cannot exceed 20 μm.
β-SiC bonded silicon carbide
β-SiC bonded silicon carbide bricks are composed of silicon carbide, silicon powder, and carbon powder in a certain proportion, mixed, shaped, and fired in a reducing atmosphere at 1400°C. Most are fired using buried carbon. During the firing process, a β-SiC bonded silicon carbide brick is produced with α-SiC as the skeleton and fine-grained β-SiC as the matrix. β-SiC is generated by the reaction between silicon powder and carbon powder during the firing process. This product usually contains small amounts of residual silicon and carbon.
Silicon oxynitride-bonded silicon carbide bricks
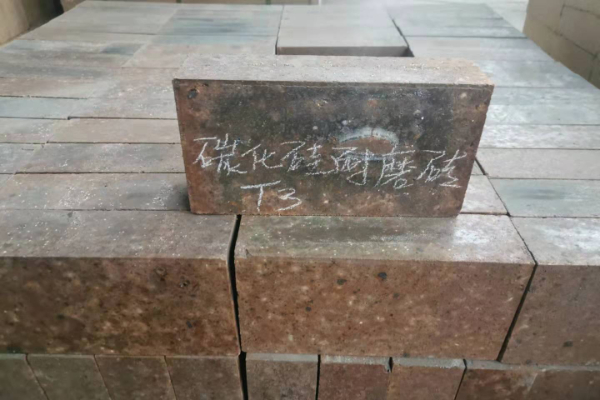
For silicon oxynitride-bonded silicon carbide bricks, the silicon powder in the ingredients is less than that of Si3N4-bonded bricks. After molding, it is fired in an N2-rich atmosphere (requiring a certain O2 partial pressure) at a temperature of 1350 to 1400°C. The finished product is a silicon oxynitride-bonded silicon carbide brick with α-SiC as the skeleton and Si2ON2 as the matrix. There are often small amounts of Si and Si3 N4 in the matrix.
Sialon-bonded silicon carbide bricks
Sialon-bonded silicon carbide bricks are made by mixing Si3N4 and Al203 powder into silicon carbide according to a certain particle size ratio, adding a binder to mix, and then firing in a reducing atmosphere after molding. Refractory products with α-SiC as the skeleton and Sialon as the matrix are produced. Since the Sialon matrix exists between the particles, the strength of the product is improved and the thermal shock resistance is enhanced.
Recrystallized silicon carbide products
Recrystallized silicon carbide products are composed of 100% α-SiC and have no second phase.
The raw material contains more than 99.5% Sic. It adopts particle gradation with maximum packing density, and high-pressure molding, and is fired in an electric furnace that is isolated from the air. The temperature is above 2100°C. The electric furnace is required to be burned to 2500°C. SiC evaporates and condenses, resulting in a Shrink-free self-binding structure.
WeChat
Olvassa be a QR-kódot a wechat segítségével