Selection of heat-resistant materials for different types of boilers
As an important equipment for energy conversion, the stable operation of boilers is inseparable from the high-temperature and corrosion-resistant refractory lining. Depending on the type of boiler, such as coal-fired boilers, biomass boilers, gas boilers, and circulating fluidized bed boilers, the performance requirements for tűzálló anyagok are also different. Correct selection of matching refractory materials can not only extend the life of the boiler, but also improve thermal efficiency, reduce energy consumption and maintenance costs.
Starting from the structural characteristics of common boilers, this article will introduce the performance requirements of various types of boilers for refractory materials and recommended material selection suggestions. It is hoped that it can provide practical reference for boiler manufacturers, operation and maintenance units and industrial users.
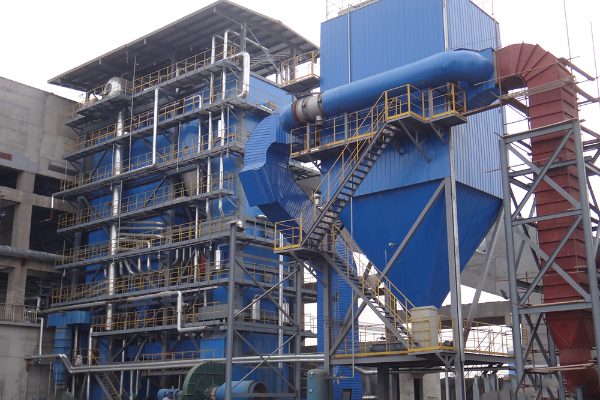
Introduction to the selection of different boiler heat-resistant materials
The main purpose of using wear-resistant refractory materials as lining for circulating fluidized bed boilers is to protect the furnace steel shell from being eroded and worn by the burning materials.
The most commonly used castables for boiler lining are amorphous castables, refractory and wear-resistant castables, plastic castables, low cement castables, corundum castables, steel fiber refractory castables, lightweight castables, stb.
The power generation boiler consists of a combustion chamber, water-cooled tube wall, superheater, economizer, preheater and steam drum. The temperature of the combustion chamber of the power generation boiler is about 1550℃. The combustion chamber has a steam-cooled wall in the high-temperature flue of the water-cooled tube near the furnace wall, so the temperature inside the furnace wall is not high. Általában, it does not exceed 900℃. If the furnace wall is a membrane water-cooled wall structure, the temperature is only 500-600℃. Or even lower.
If it is a chain furnace or a pulverized coal furnace, the operating temperature is about 1000℃. If it is a fluidized bed boiler, the temperature is higher and many pipes pass through the furnace wall. Ebből adódóan, the grade of refractory castables used for the lining of fluidized bed boilers should be high.
If it is a light-duty boiler, the working layer of the furnace lining is generally made of clay refractory castables or clay refractory plastics as the lining, and the heat insulation layer is made of lightweight castables for insulation, and also made of insulation boards or fiber cotton; some manufacturers will apply a sealing layer on the outer surface of the furnace skin to enhance the air tightness of the boiler lining. This is more heat-insulating and saves fuel.
The pulverized coal furnace is flushed by pulverized coal particles and airflow at the same time, cast with high-aluminum and clay refractory castables, and the furnace top is rammed with high-aluminum refractory plastics. In the case of severe wear of coal particles or erosion by dusty airflow, high-wear-resistant castables, vagyis, silicon carbide refractory castables, are used as the working layer lining to increase its service life.
If the boiler uses tűzálló téglák, it is used in the return device of the circulating fluidized bed boiler, the furnace wall of the economizer, the inner wall of the mixed asphyxiation, the flue, the chimney lining, stb.
Refractory and wear-resistant castables are mainly used for boiler cyclone separators, furnaces, dense phase areas, furnace outlets, water-cooled air chambers, slag coolers, return devices, ignition air ducts, stb. High-aluminum refractory castables are used for boiler smoke corners, wind chambers, economizer guard plates, fire doors, stb. Lightweight insulation castables are used for boiler tops and furnace wall insulation;
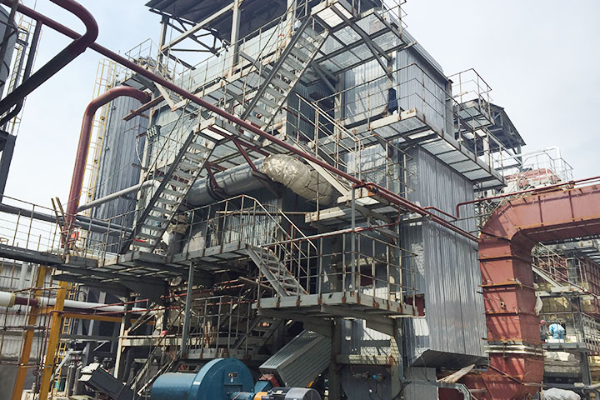
Wear-resistant plastics are easy to construct, quick to repair, high-strength and wear-resistant, Jó hőkancia -ellenállás, nincs repedés, és jó tömítési teljesítmény. They are mainly used for the repair and local tamping of fluidized bed boilers; micro-expansion refractory plastics have strong plasticity at room temperature, strong adhesion, high strength after natural drying, micro-expansion at high temperature, high fire resistance, good sealing performance, and convenient construction; corrosion-resistant and wear-resistant ramming materials have good thermal conductivity, which is conducive to heat conduction and are used in the parts of circulating fluidized bed furnaces that require wear resistance and corrosion resistance;
WeChat
Olvassa be a QR-kódot a wechat segítségével