Application of baking-free castables in blast furnaces
For blast furnaces with only a single taphole, the tapping interval is short, and the wind-off time is short. If low-cement castables are used, sufficient baking time cannot be guaranteed, so most of these blast furnaces still use unbaked iron ditch ramming materials. Unbaked ramming materials have the disadvantages of loose structure, poor oxidation resistance, low iron throughput, and high labor intensity of on-site construction. In addition, there are also those that use prefabricated iron ditch parts for splicing and installation, but there has been no good solution to the joint treatment problem. সুতরাং, how to effectively solve the life of the taphole of a single taphole blast furnace has attracted much attention. To this end, after a lot of analysis and research on the working conditions, damage mechanism, chemical composition of molten iron and slag of the blast furnace taphole, an baking-free castables suitable for the blast furnace taphole has been developed.
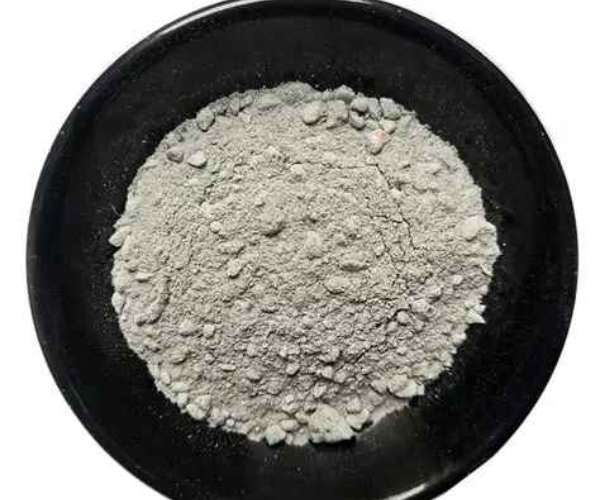
No-bake castables and low-cement castables
When the water content of ordinary low-cement castables is high, the water will be discharged in large quantities and quickly when the temperature rises sharply. When the water discharge channel is blocked, the water cannot be discharged in time, and the steam pressure surges, which will cause the material to burst. This material has the following problems:
① Since alumina cement is used as a hardener, the introduction of CaO causes the matrix to have a low melting point, which reduces the corrosion resistance;
② Adding a drying aid metal Al powder, the addition of metal Al powder is effective for drying, but the construction body is prone to cracking, which leads to a tendency of tissue deterioration;
③ Phosphate-bound materials have a binder migration problem, which causes ion enrichment on the material surface, blocks the pore channel, and is prone to layering, bursting and peeling.
The design idea of baking-free castables is to use the characteristics of dense castables and convenient construction, use non-aqueous liquid organic compounds as fluidity imparting agents and binders to ensure the construction fluidity of castables, and add alkaline materials as hardeners to the mixed refractory bulk materials for stirring to obtain a material with fluidity that can be vibrated for construction. After casting, it is hardened and demolded in a very short time at room temperature or under the residual heat of the trench. Since the moisture content of the material is very low, it does not need to be baked and can be directly tapped, achieving the purpose of reducing operation time, reducing labor intensity, and increasing the service life.
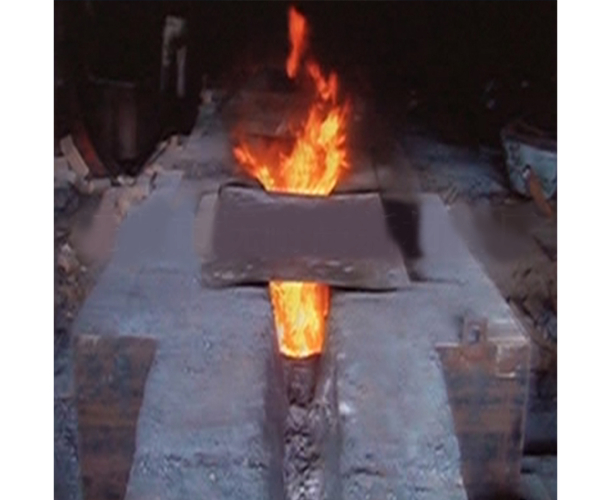
The materials for the iron ditch must have high performance such as corrosion resistance and wear resistance. The materials used in our products are composed of raw materials with strictly managed particle size as aggregates, and a mixture of clay and various binding materials that can produce hot strength in various temperature ranges, including fused brown corundum (good corrosion resistance and wear resistance, strong resistance to molten iron. In order to increase the service life of the ditch material, the porosity of corundum should be low), carbon and silicon carbide (small volume change with heat resistance, difficult to be wetted by molten iron and slag, chemical stability, carbon can adapt to iron and slag, and silicon carbide is more suitable for slag), binding materials (non-aqueous liquid organic compounds, binding materials that can maintain strong organizational strength from low temperature to high temperature, ensuring sufficient strength of the material), and antioxidants, dispersants and other additives are added to improve material properties.
In order to fully understand the anti-explosion performance of the material, an explosion-proof test of an enlarged sample was carried out.
(1) Mixing: Add 6% of PBH88 liquid to the premixed materials until they can be cast and formed. Discharge after stirring evenly. The semi-dry materials at the discharge port should be returned to the pot and stirred twice before formal use to ensure uniformity.
(2) Casting: In order to simulate the residual heat of the trench body on site, the stirred slurry is quickly poured into the preheated mold (coated with release agent) and vibrated and formed using a vibrating rod. Under the condition of residual heat, the material has good construction workability. Vibrate until the surface is slurried and the exhaust is sufficient.
(3) Rapid baking: After the prefabricated parts are formed, they are basically hardened by natural curing for about 1 ঘন্টা. They are placed on the explosion-proof test bench built in advance to simulate the site. The outer template is not removed, making it more difficult to discharge the gas. The test conditions are relatively harsh. A sufficient amount of burned coke is stacked in the core mold of the prefabricated parts, and then they are directly baked for 30 minutes by blowing air and oxygen. The highest temperature measured is above 1400℃. No explosion occurs, and no obvious cracks are found, which fully meets the requirements of no baking.
Rongsheng baking-free castables
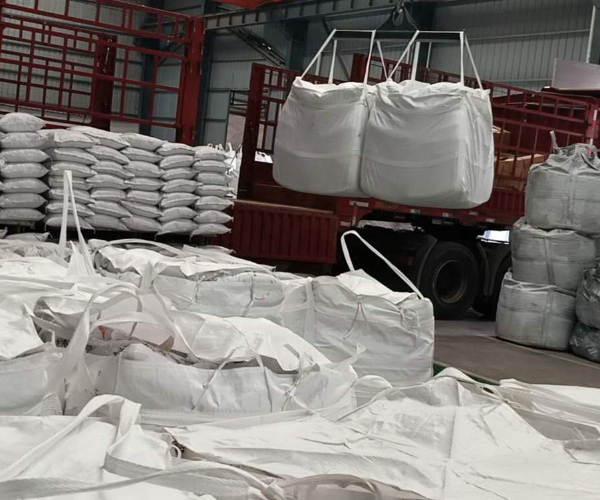
The baking-free castables for blast furnace tapping ditch produced by Rongsheng Company can completely replace the existing ramming materials and prefabricated parts, and can achieve the requirements of high production, increased efficiency and reduced consumption of blast furnaces, and reduce the labor intensity of furnace workers. On-site feedback shows that the material does not stick to slag iron during use, is easy to clean, and has a good service life, bringing huge economic benefits to the ironmaking plants of various steel companies.
WeChat
Wechat দিয়ে QR কোড স্ক্যান করুন